Starion
turbochargers |
|
|
Starions used 6 different turbochargers
depending on engine and market
1) TC06-11A (8 cm2 turbine housing) non intercooled
4G63 2.0 litre SOHC (Australia, JDM, Europe)
2) TC06-11A (8 cm2 turbine housing) intercooled
4G63 2.0 litre SOHC (Australia, JDM, Europe)
3) TC05-12A (6cm2 turbine housing) non intercooled
JDM 4G63 2.0 litre SOHC (JDM)
4) TC05-12A (6cm2 turbine housing) intercooled
JDM 4G63 2.0 litre SOHC (Australia, JDM)
5) TD05-12A (8cm2 turbine housing) non intercooled
4G54 2.6 litre (USA, JDM, Europe)
6) TD05-12A (8cm2 turbine housing) intercooled
4G54 2.6 litre (USA, JDM, Europe)
The intercooled and non-intercooled turbos
had the same wheels but the compressor housing was different.
The compressor outlet was different to enable connection of the
intercooler hose. Because of this the wastegate actuator was
also different.
Also there were watercooled and non-watercooled
versions for some models.
|
|
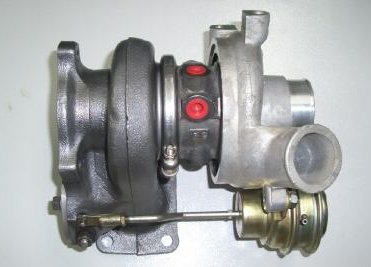 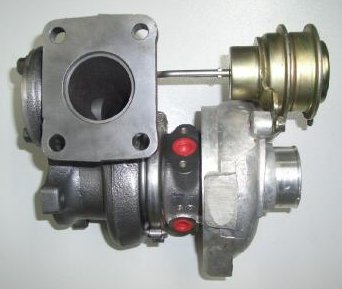 |
TD05-12A turbo (with intercooled
type compressor housing) |
|
Turbo
comparison and identification |
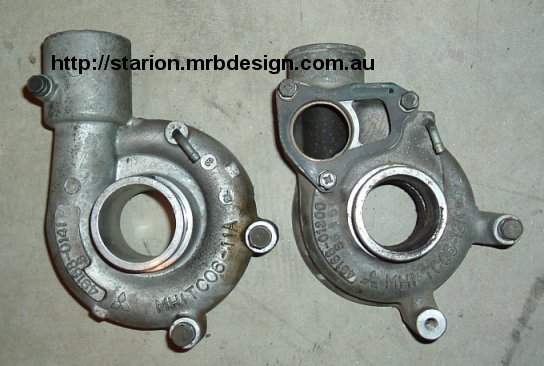 |
Turbo compressor housings.
Australian JA,JB Starion uses 4G63
SOHC engine with a TC06-11A (left hand pic)
Various Japanese domestic market (JDM)
4G63 SOHC used TC05-12A.
|
 |
TC06-11A compressor wheel on the left
TC05-12A compressor wheel on the right. |
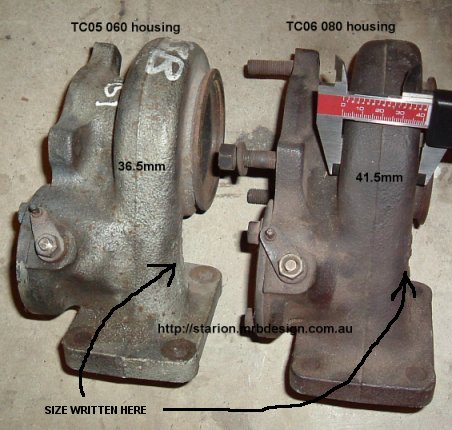 |
JDM TC05 housing compared to
TCO6. Dimension shown only to highlight obvious external size
difference of the housing and hence internal size/area. |
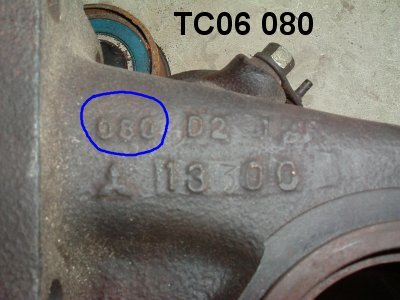 |
Identification number are on
the housings |
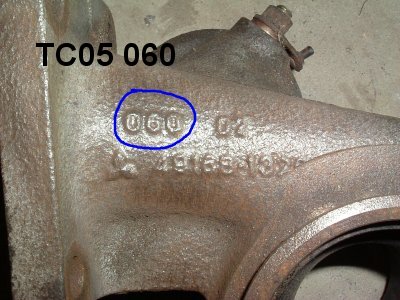 |
|
Australian
spec 4G63 SOHC 2.0 Starion used TC06-11A turbo with 8cm2 (080)
exhaust. The US market G54B 2.6 Starion/Conquest used the TD05-12A
however with a 8cm2 (080) exhaust housing. The Japanese market
4G63 SOHC 2.0 Starion used a TC05-12A (same size turbine wheel
as US) however with the much smaller 6cm2 (060) exhaust housing. |
|
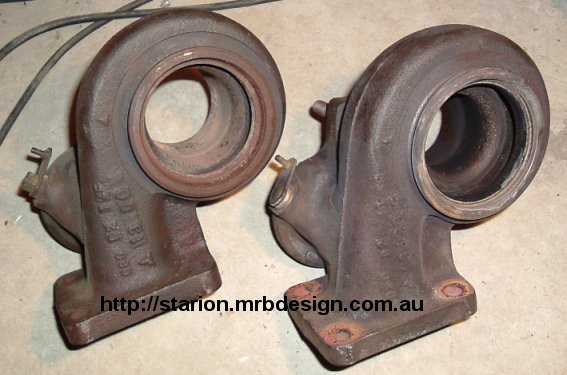 |
TC06 turbine 8cm2 (080) housing
on the left and TD05 8cm2 (080) housing on the right. |
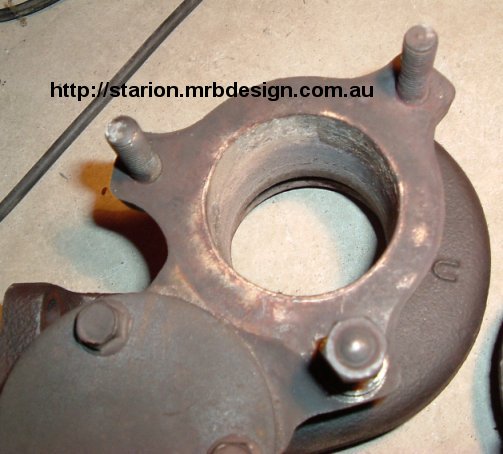 |
TC06 turbine 8cm2 (080) housing
as used on 4G63 2.0 SOHC 8 valve Australian spec Starions. |
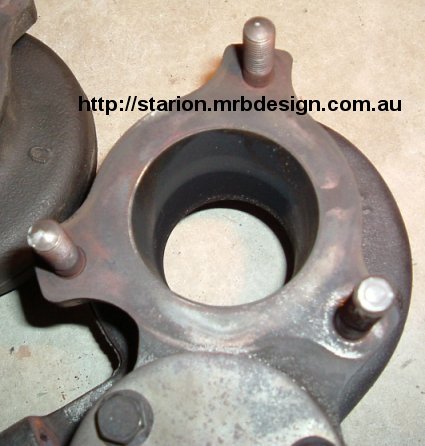 |
TD05 turbine 8cm2 (080) housing
as used on G54B 2.6 US Starion/Conquests
. Notice smaller diameter. Entry slot
into involute is also 1mm narrower.
|
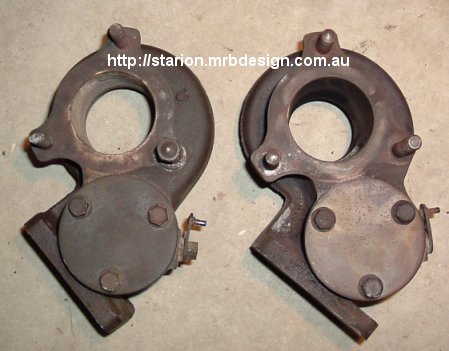 |
Another shot TC06 on the left
TD05 on the right. |
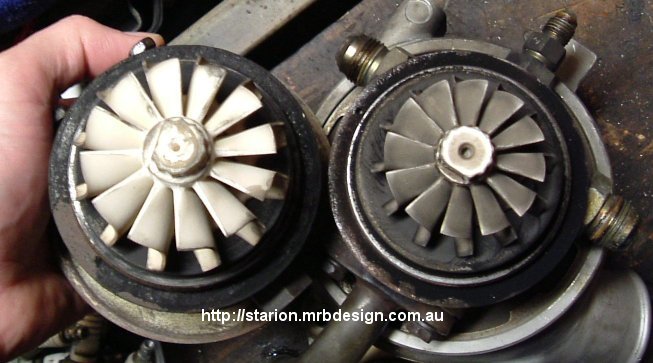 |
TC06 turbine wheel on the left
and TD05 turbine wheel on the right |
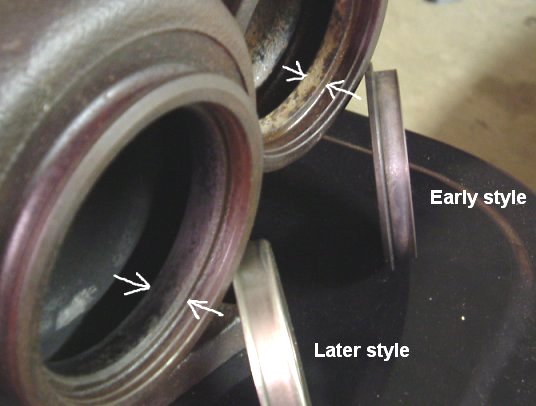 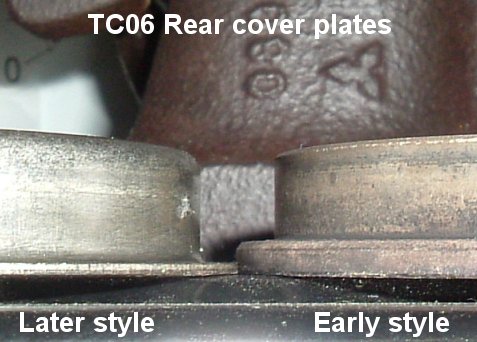 |
There are minor differences
between early and late TC06 turbine housings. However the centre
cartridge is the same and is interchangable providing the correct
cover plate is used.
(Note: to change the cover plate the
turbo centre cartridge has to be pulled apart)
|
|
Special Stuff |
|
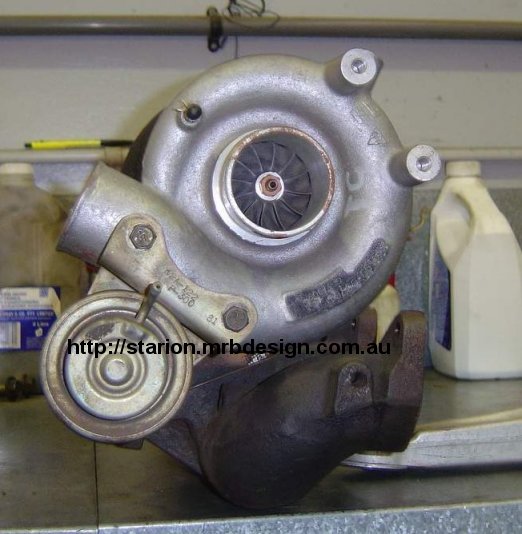 |
Ralliart TD06-19C turbo used
on factory Pajero/Starion G54B 2.6 litre 330hp spec race engine.
This is the same turbo used on 1988 Paris-Dakar Ralliart Pajero.
These turbo's were used by the factory
teams only and were not for sale.
Wastegate actuator has only a 300
Kpa (0.3 bar) spring. Boost was controlled by the ECU. This could
be changed in the cockpit by means of a switch.
|
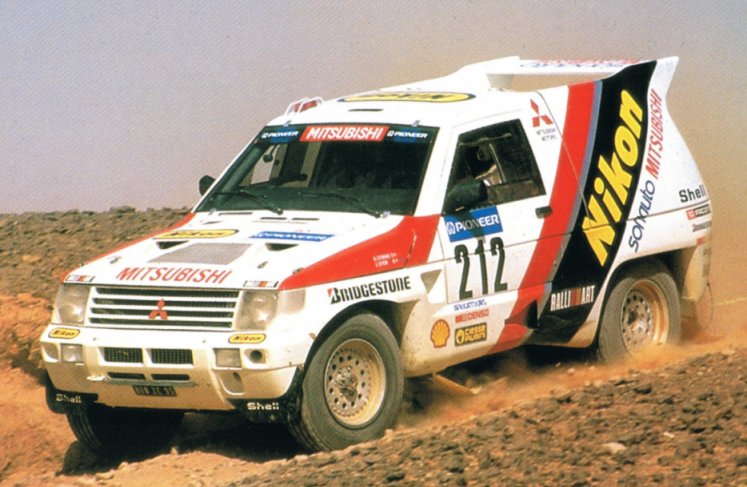 |
1988 Paris-Dakar Ralliart Pajero!
Full kevlar body spaceframe construction
200Km/h + on the sand!
|
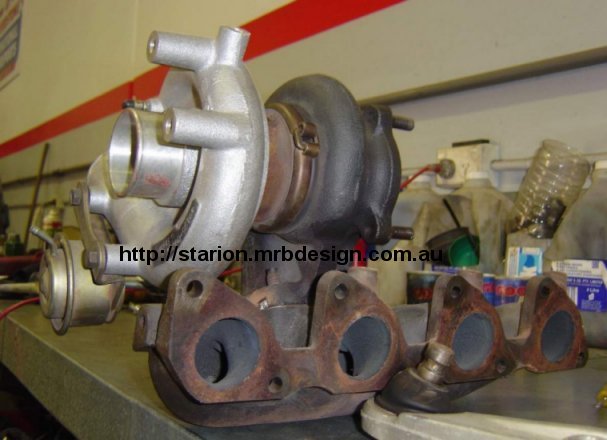 |
Side view. Note lack of water
cooled centre bearing housing. |
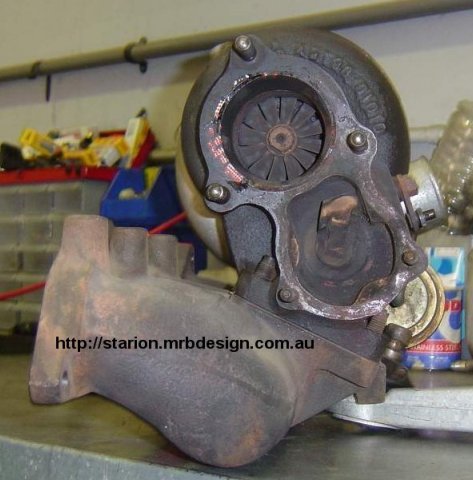 |
Rear view. A separate pipe was
used for the wastegate and joined the main exhaust about a metre
down the engine pipe. |
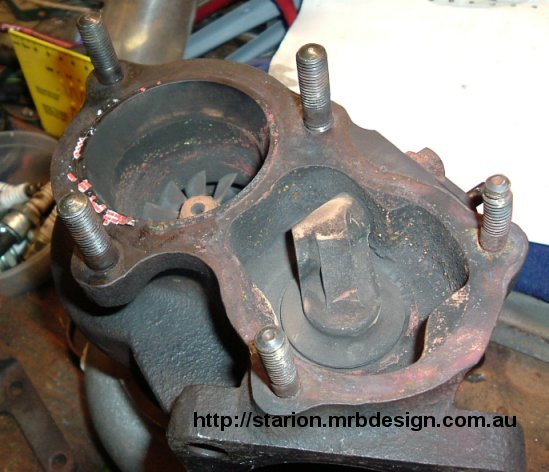 |
This view shows there is no
provision for wastegate passage to main exhaust outlet so seperate
dump pipe for wastegate must be used. |
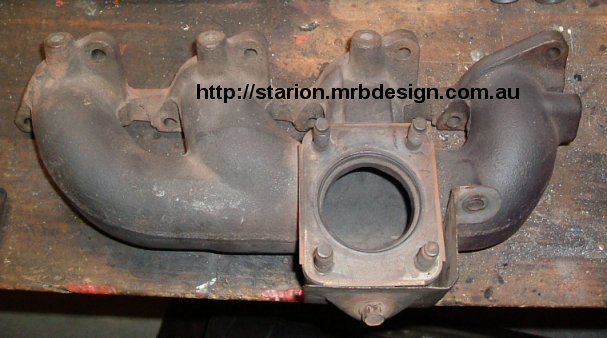 |
This is the Ralliart exhaust
G54B 2.6 manifold shown with the turbo above. Notice size of
turbo outlet. |
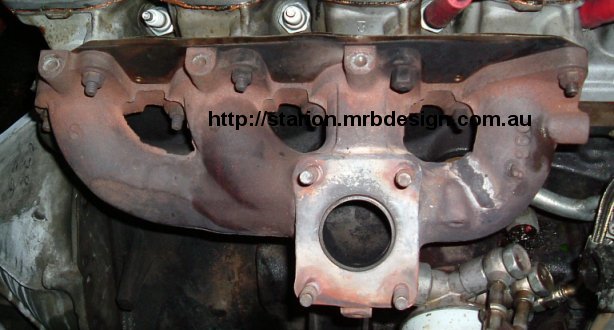 |
This is a standard 2.6 G54B
turbo exhaust manifold.(notice weld repair) |
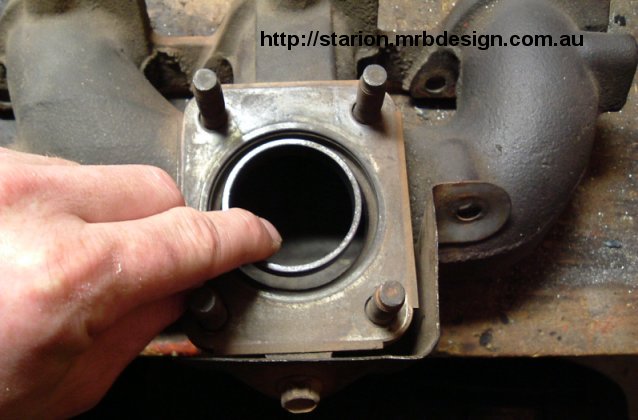 |
This view shows the sealing
ring from the standard G54B manifold above you can see how much
bigger the Ralliart manifold turbo outlet is.
ID on standard manifold is 43.2mm.
Ralliart manifold is 54.2mm.
|
|
|
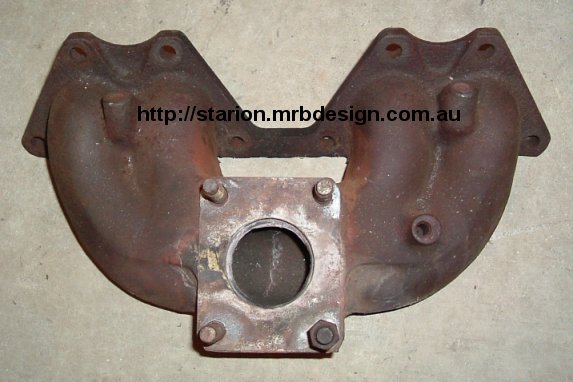 |
This is exhaust manifold
from 4G63 2.0 SOHC engine. Turbo outlet is exactly the same size
as stock G54B. |
|
Turbo Testing
I did some testing before and after
fitting the Ralliart TD06-19C. The first graph shows data recorded
using the "high flowed" TD05. Compressor housing was
modified and a Garrett compressor wheel was fitted. Turbine side
was stock. My horsepower has increased by somewhere around (I
say around because the previous best with the TD05 was 180HP
and the test was done in 4th gear) 40HP at the wheels with NO
other changes other than to connect the different exhaust flange.
I'm running a ported Magna head, Camtech cam (Camtech is an Australian
cam company), full 3" exhaust, standard ECU, standard airflow
meter. Being an engineer I decided to do some data logging to
see what the difference was between the turbos. See graphs below.
Due to my limited budget I purchased low cost DAQ gear that could
only sample at about 6-8 samples a second that's why the graphs
have steps but the info is still there to see. There is no RPM
trace on the graphs so I added some RPM markers.
|
|
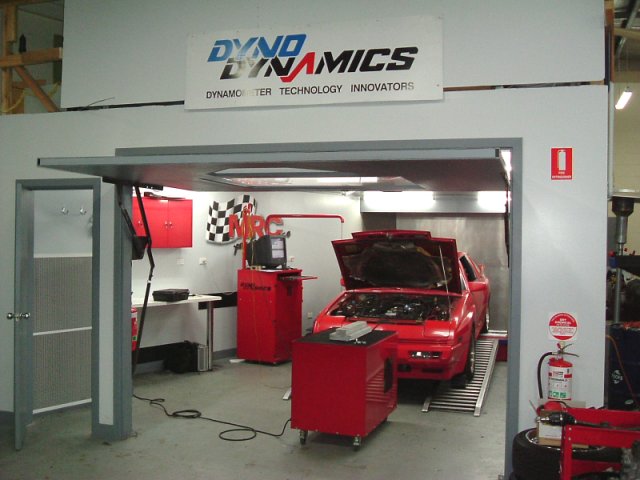 |
Starion on the dyno at MRC Dyno
located in Sydney Australia. |
|
Engine bay pic with TD06 turbo
fitted. |
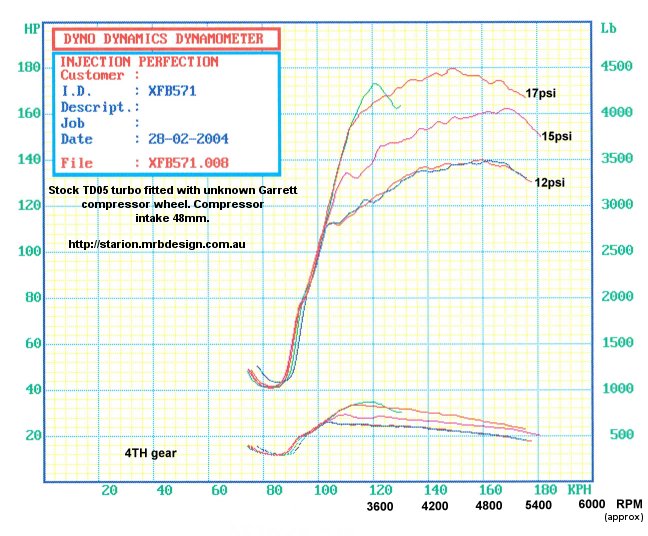 |
TD05
Dynosheet
|
|
TD06-19C
Dynosheet
|
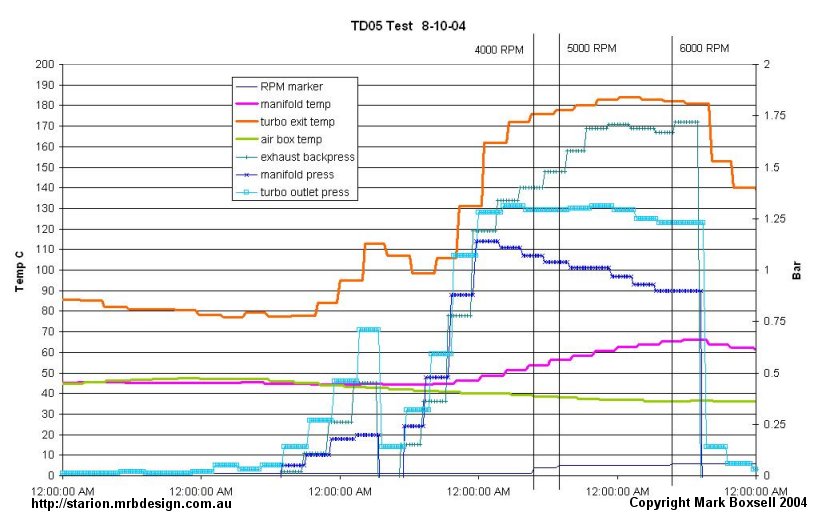 |
NOTE: TDO5 was "high flowed"
and fitted with a Garrett compressor wheel by previous owner.
Turbine side was untouched. |
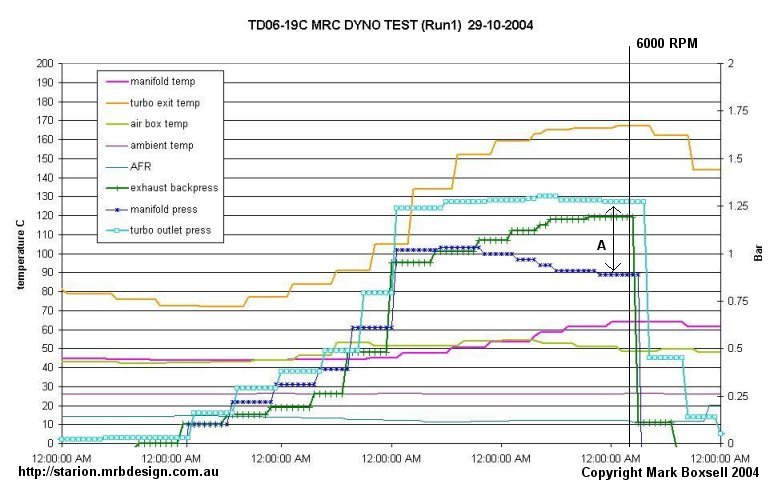 |
Note it is making 221 HP on
only 13 psi. |
The main difference between the turbos was:
1) Reduction of exhaust manifold backpressure by 0.5 bar (7.25
psi) @ 6000 RPM!!!!
Uncorked!!!!
2) Reduction in compressor outlet temperature
of approx 20 degrees C
Note: this is with a lot higher airflow as well.
Another discovery is the major restriction
between the turbo outlet and the inlet manifold. There is about
a 3.8 psi pressure drop through the TBI (with 220HP airflow)
noted as "A" in the graph.
The engine wants to really rev now pulls hard
to 6500 RPM even with the boost dropping off as shown in the
graphs. Note the wastegate is connected to the "hard pipe"
so keeps the pressure constant there.
|
|
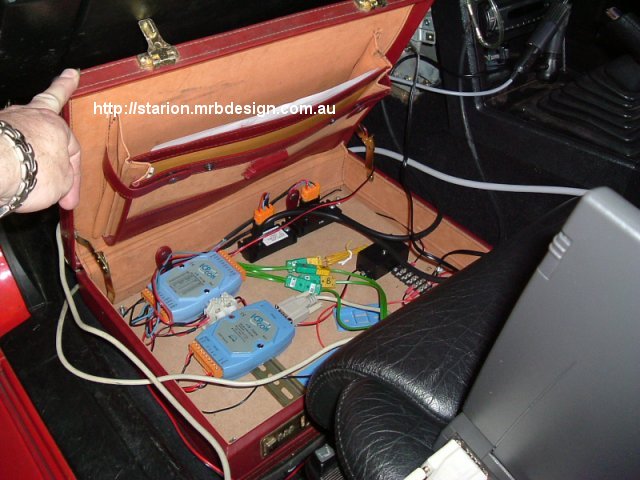 |
Briefcase DAQ system I built
using 3 bar Delco MAP sensors, M&W Uego wideband controller
(not shown) and ICP i7000 modules. |
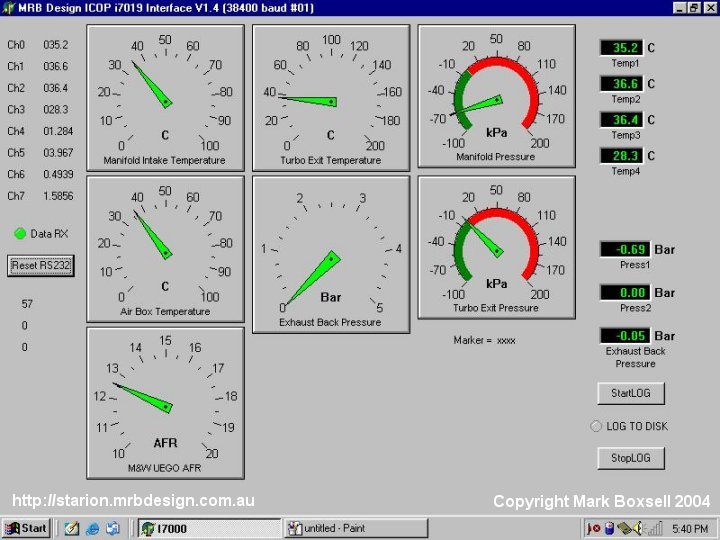 |
I wrote the software using Borland
Delphi. |
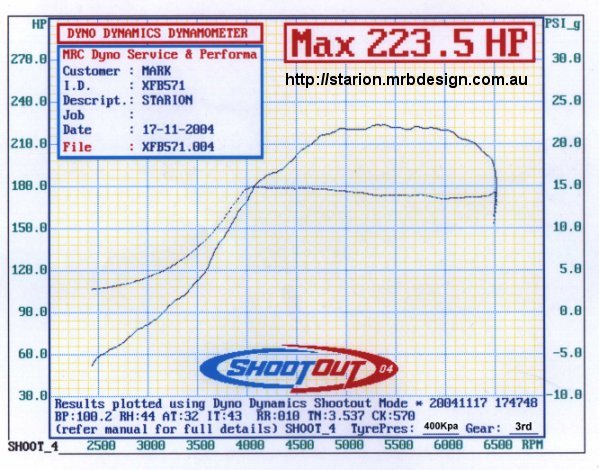 |
Another run with a fraction
more boost and the wastegate hose relocated to the inlet manifold
(was in cross-over pipe).
Note: abrupt roll off at 6500 RPM
is dyno operator backing off.
|
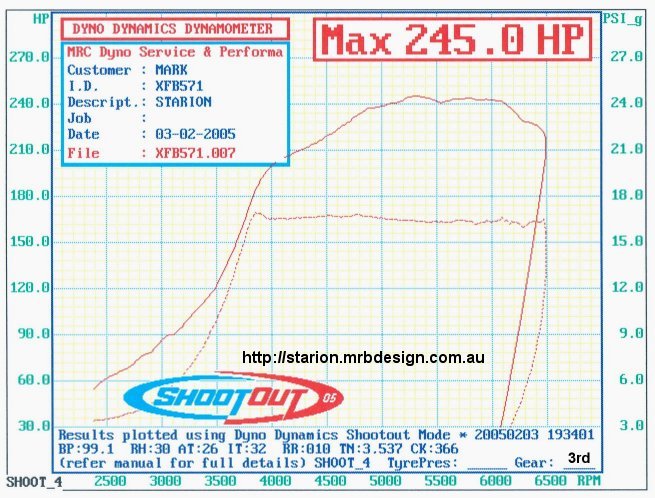 |
HKS EVCIV fitted boost increased
to17 psi with factory air cleaner removed and POD filter (no
airflow meter) and Haltech F3. |
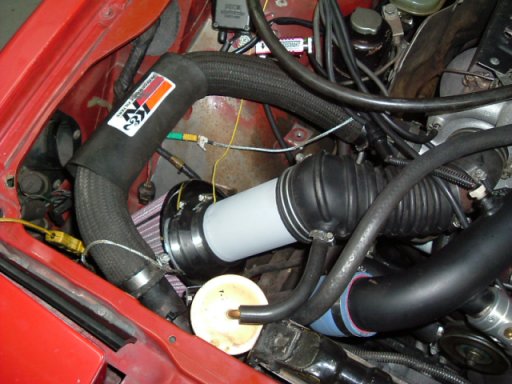 |
POD filter could be installed
better but was installed quickly for dyno run. |
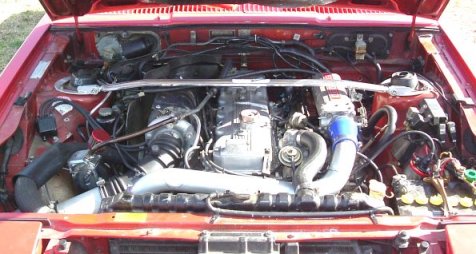 |
Magna MPI
installed
|
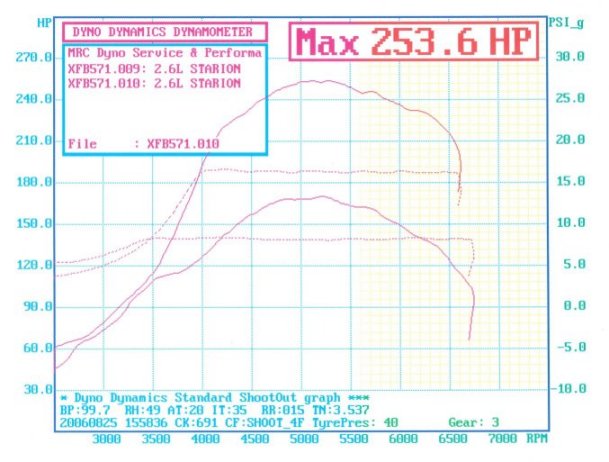 |
Magna MPI
dyno sheet.
This does not tell
the whole story the
drivability is vastly
better compared to
the stock TBI setup.
|